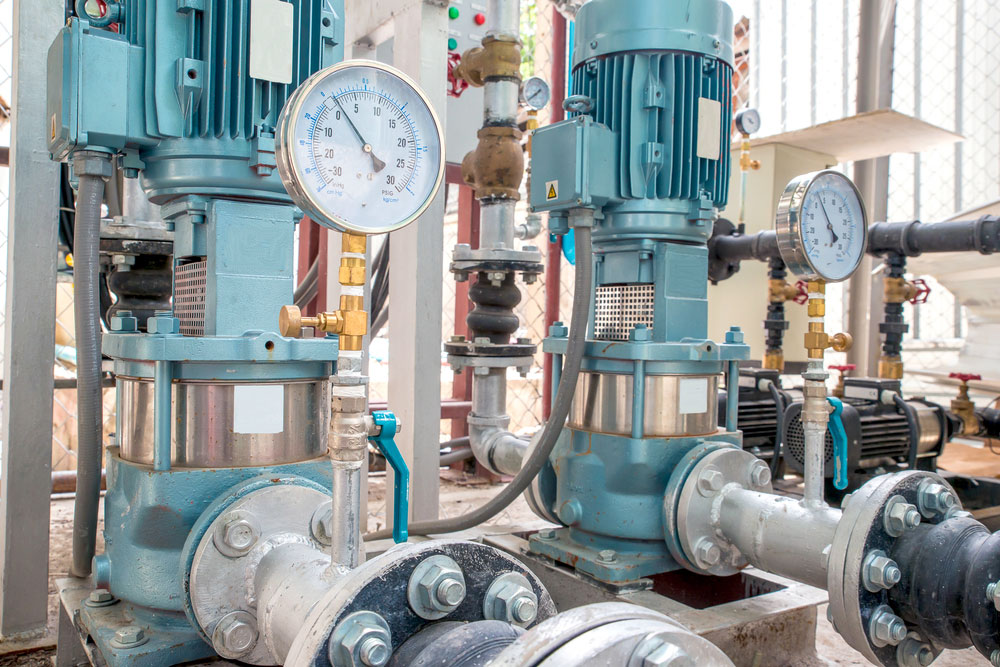
Product Description
Condensate return pumps are used to move water from the main condenser hotwell through several intermediate components (such as the condenser gland steam system and the ejector air removal system) back into the boiler feedwater system. Seemingly a relatively simple and straightforward application, condensate return pumps must in fact be carefully specified to consider factors such as wide variations in turn down and very low NPSH requirements, and the need to integrate with the hotwell level control system. MVT offers a line of custom designed condensate pump systems in duplex, triplex, and quadruplex configurations to meet these requirements. We work closely with a few select pump suppliers to design a system that will work automatically to maintain proper level in the hotwell under varying load conditions. These are ‘plug & play’ packages that include isolation valves, non-return valves, vibration isolators, by-pass control valves (when needed), manifolds, and instrumentation for a complete, engineered solution. Options include control panels with logics, motor starters, and level control instrumentation for remote monitoring and control.
Key Features & Benefits
Key features and benefits of our condensate pump systems for the plant are:
- Full range of capacities available for any main condenser requirement.
- Careful matching of pump performance with level control requirements.
- Compliance with typical industry standards such as ASME, ANSI, PED, CRN, etc.
- Innovative package designs, with ‘single point’ customer connections for all process and utility requirements.
- Control system integration with hotwell level controller.
- Typical Power Industry quality component suppliers, with ASME code qualified welding throughout.
- Comprehensive field service and support program.
- Industry leading 3 year warranty.
